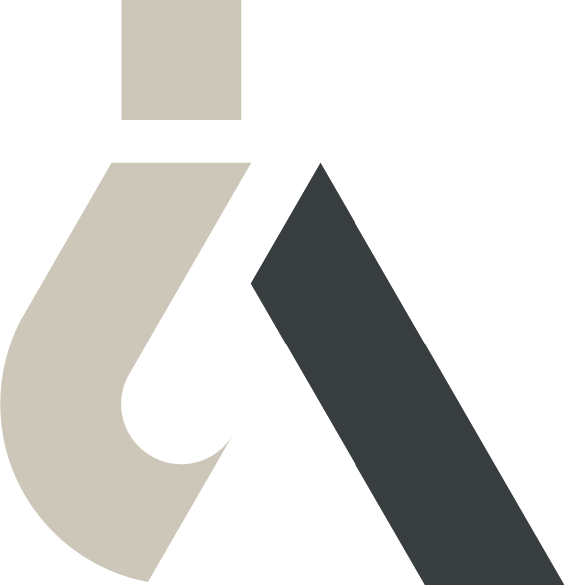
Cyclones (cyclone separators) are used in manufacturing mainly for air pollution control and material recovery. They employ high-speed rotating airflow to separate particles from gas streams, using centrifugal force to move heavier particles outward toward the exterior wall where they fall into a collection chamber while the cleaner air exits through the top.
Cyclones are used in many industries and in conjunction with other systems and manufacturing processes. They include:
Cyclones are also integrated with other air pollution control devices. Combining cyclones with baghouse filters, electrostatic precipitators, or wet scrubbers provides multi-stage filtration systems to capture a broader range of particulate sizes and types, ensuring cleaner emissions and improved air quality.
There are several important design factors to consider during the selection process to ensure cyclones function properly and meet application requirements.
Air/Gas Conditions – the condition of air/gas moving through the system affects cyclone sizing, configuration, and construction. Properties include air temperature, moisture content, and pressure.
Particulate Characteristics – as particle separators, cyclone design is dependent on particle characteristics. These characteristics include particle size, type, specific gravity, bulk density, specific gravity, and more.
System Requirements – industrial operations have different process requirements, and these impact cyclone design customizations. System size, positioning, and clean air requirements determine the necessary airflow and pressure drop for proper cyclone sizing.
Fan Selection – centrifugal fans are key components to most cyclone systems. Fans designed with the correct velocities and inlet sizes allow for fewer transitions and eliminate “dead spots” in the system, boosting performance and decreasing duct maintenance.
Cyclones are robust and low maintenance. If these design considerations are factored into your system design, you can expect your cyclone to provide many years of continuous service.
Our team and partners have designed and built thousands of cyclones for countless industrial applications. Reach out today, and our engineers will help you as well!